Quality Management Systems
At GPSS, we are committed to ensuring the highest quality standards across our global supply chain. Here, you can find detailed information on how we achieve and maintain these standards.
Through our comprehensive Quality Management System, we ensure product quality through rigorous inspection, accurate sampling, and thorough testing.
Our international team conducts factory qualifications, part approvals, and ongoing supplier management to ensure continuous adherence to our high standards.
Supplier Selection and Evaluation
We implement a selection process that includes onsite audits and confirmation of factory certifications. These audits are conducted locally by GPSS employees, ensuring a thorough evaluation of suppliers.
Maintaining Consistent Standards
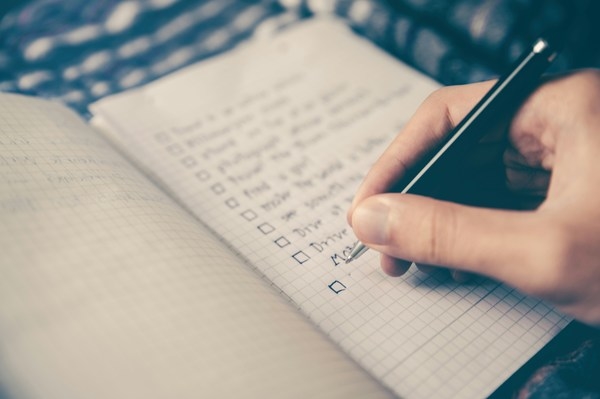
We use a combination of detailed checklists, frequent audits, precise inspections, and proactive feedback mechanisms. Our team in the US collaborates closely with our overseas team to maintain these high standards. Regular training sessions and workshops are held to ensure that all team members are up to date with the latest quality management practices.
Quality Control and Assurance
We focus on extensive training of personnel and conducting in-process checks and testing at both the factory and our US manufacturing location. By reviewing control plans and processes, we ensure that our factories maintain robust quality control plans. Our Quality Assurance team continuously monitors production processes to preemptively identify and address potential issues.
We address issues through structured corrective actions, detailed 8D reports, and thorough root cause analysis to identify and resolve the underlying causes of any discrepancies. This proactive approach helps in preventing future occurrences and ensures continuous improvement.
Inspection facilities located in the US as well as in our international engineering offices helps ensure part and process quality.
Certifications and Standards
Our factories adhere to the ISO standard quality management system, ensuring that we meet internationally recognized quality benchmarks. Our manufacturing facilities are automotive and medical industry certified. We also stay in compliance with various industry-specific standards and regulations to cater to diverse market needs.
Client Collaboration and Compliance
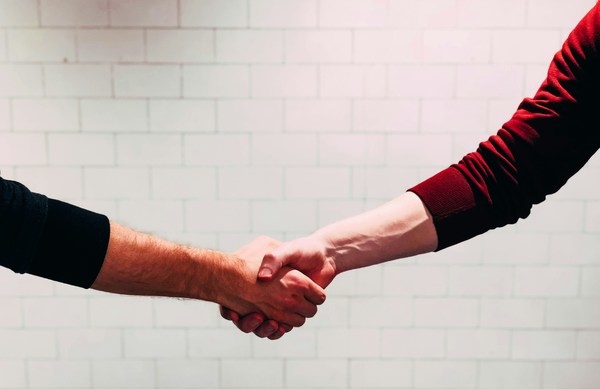
We engage in direct and transparent communication with clients through email, phone, and in-person visits. Compliance is ensured by documenting processes and procedures at factory sites, performing factory audits, and providing inspection reports for each production run. We tailor our quality management practices to meet the specific needs and requirements of each client, creating a collaborative environment that drives mutual success.