Inventory Management
GPSS is dedicated to providing our clients with efficient and accurate inventory management solutions. We offer inventory programs that range from Vendor Managed Inventory (VMI), Just-in-time (JIT), and any customized inventory management to suit your needs. Here, you can find detailed information on our approach and the strategies we use to optimize inventory levels and provide seamless operations.
The GPSS Approach
We ensure the accuracy of parts and quantities on arrival by performing periodic cycle counts as well as a yearly physical inventory. We collaborate with our customers to determine their needs and keep parts on hand ahead of the schedule indicated by the customer to safeguard part availability. Additionally, we offer warehousing services to help save our customers warehouse space and capital by holding inventory for them.
Optimizing Inventory Levels & Minimizing Carrying Costs
To optimize inventory levels and minimize carrying costs, we run a monthly over 90-day report on inventory levels based on lot number receipts. A list is sent to the customer service representative to review with the customer. We also analyze demand and forecast to make certain proper inventory levels are maintained in collaboration with the customer.
Demand Forecasting & Inventory Replenishment
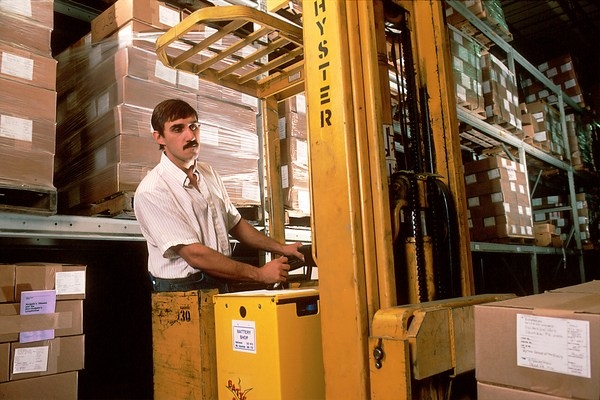
Demand forecasting and inventory replenishment are managed through a time phase report generated from our ERP system, Epicor. Our customer service representative and purchasing team review this report together to manage pull-ins and pushouts as needed with our customers, providing timely and accurate replenishment.
Technologies & Software for Efficient Inventory Management
We utilize Epicor, our ERP system, which is a comprehensive quote-to-cash solution. This advanced software allows us to track and manage inventory efficiently, providing real-time data and insights to optimize inventory management.
Ensuring Accuracy & Reliability in Inventory Data
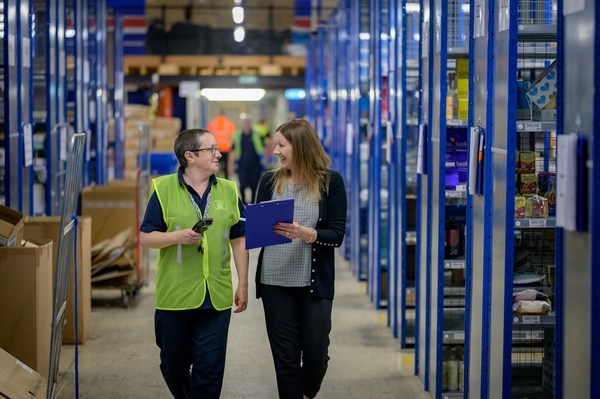
We establish accuracy and reliability in inventory data by performing periodic cycle counts and yearly inventory audits. Our purchasing team runs a time phase materials report monthly to make sure the ending inventory balance is accurate based on customer demand and expected receipts. This rigorous process helps maintain data integrity and reliability.
Inventory Risk Management & Supply Chain Disruption Mitigation
To handle inventory risk management and mitigate potential supply chain disruptions, we review the time phase report for expected receipts and demand. Based on this evaluation, we expedite or push out deliveries as necessary to maintain a smooth supply chain operation.
Collaboration with Clients for Continuous Improvement
Our customer service representatives are in constant communication with customers to ensure any changes to demand are reported to the purchasing team. This allows us to expedite, slow down, or cancel orders as needed. We also facilitate cost reductions by offering blanket order options with release dates executed by stocking agreements, helping clients save costs and improve inventory management processes.